Company Overview
Proto Ltd. is one of the few big producer of knitted fabrics in Bulgaria. Their production is separated in two factories situated in two different towns - one of the factories houses the knitting and the other - the dyeing and finishing of the fabrics. Bearing in mind the specifics of such an organization, the effective communication between those two factories is crucial for the company’s success. This leads the owners to the idea that they need a fully-integrated system to organize, record and track all of the production processes and work simultaneously in both factories.
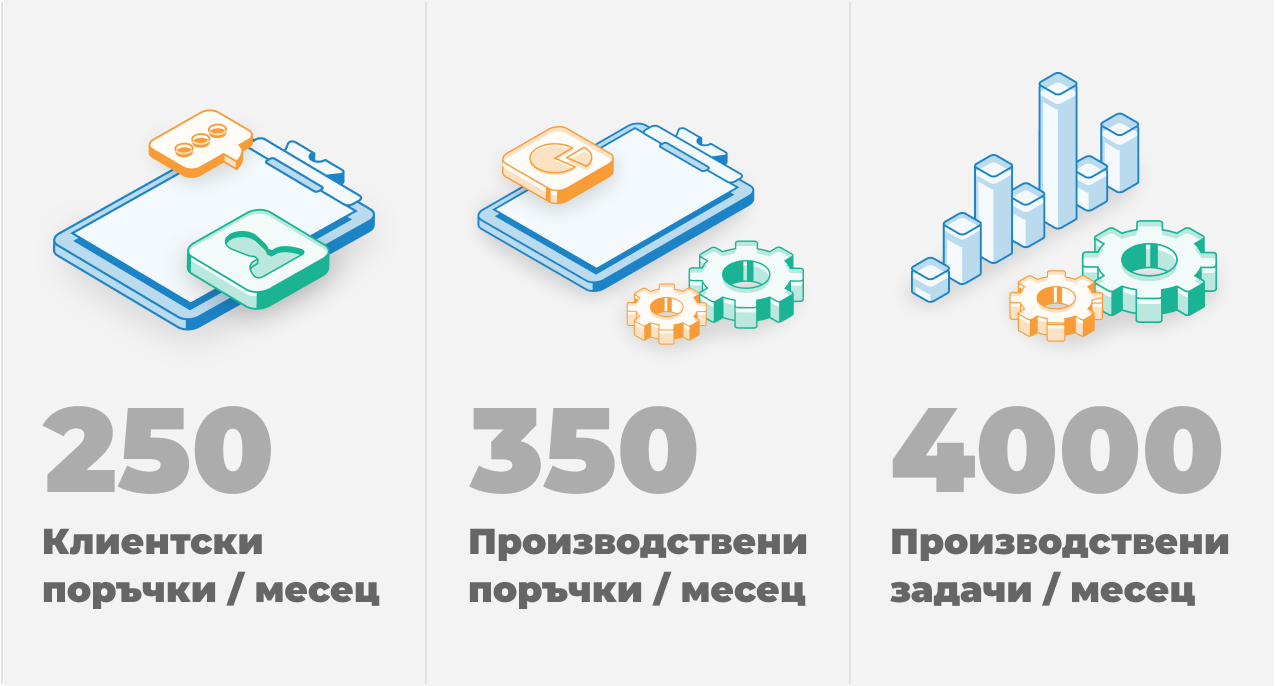
The Challenges
Some of the challenges that Proto were facing:
- How to accomplish better and more efficient communication between the two factories?
- How to organize the orders and transfers of loomstate fabric between the factories?
- How to keep track of the orders for loomstate and finished fabrics as well the materials used for their production?
- How to facilitate tracking of batches for the available loomstate fabrics and link those batches with the materials and resources for their production?
Tracking the batches of loomstate fabrics was the main case we needed to solve. This is an extremely important process for us. The solution prevented us from using fabrics from different batches thus increasing the quality of the finished goods.
Nikola Harsev, Production manager, Proto Ltd.
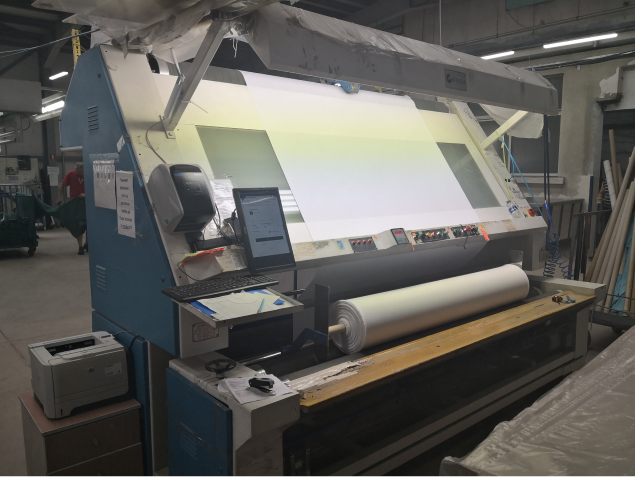
The Solutions
After a comprehensive analysis of the processes, the workflow and the challenges in Proto, we suggested to go on with stage-by-stage integration of TOWERP.
We started the implementation from the loomstate factory where the problems were more urgent.
What we did first:
- Full integration of the system with the electronic scales and label printers.
- Management of the transfers between the warehouses of the two factories.
- Installation of TOWERP Mobile app for inventory management on smart mobile devices.
- Loomstate batch tracking linked with the materials and machines used for their production
We then moved on to the second production base:
- Installation of mobile working stations on all machines. This enabled the workers to record on touch screens when they start and finish working.
- Stage-by-stage integration until we covered all of the business and production processes in the whole company.
These are only part of the solutions we offered. We made some new add-ons for automations as well in order to accomplish the desired optimization.
The Outcome!
The integration of TOWERP brought in some improvements and to a large extent optimized the work of both factories and the communication between them. We are now able to track the progress of each order and find where difficulties occur. The links between the client order on one hand and the production order and lot cards on the other improve the offering process and give us tools to better serve our customers
Nikola Harsev, Production manager, Proto Ltd.
We developed some new functionalities in the system for Proto. These functionalities utilized the optimization and significantly reduced the time for certain tasks.
What did we really accomplish?
- Well-organized catalogue with products, details and materials.
- We implemented several thousand items with batches in one system
- The loomstate requests are executed with just 2 button clicks
- Material transfers between both factories are reduced to one button click. This happens in real time and is a fully traceable process.
- Every fabric roll has an unique serial number, which holds all the information about it all the way to the batch numbers of the yarns used.
- Thanks to the simplified method for materials request, the planning and production of loomstate and finished fabric is fully optimized - avoiding delays of WIP units production and overstock.
- The Mobile app enables real-time listing of all the items prepared for shipment. This guarantees accuracy and saves 1-2 working days per month to the people in the warehouse.
- The mobile devices are user-friendly and do not interfere with the workflow.
The improvements in Proto continue and together we expect even more measurable results to be seen in their organization.
- To what extent will the mistakes be reduced?
- How much will they be able to speed up the offering and planning process thanks to TOWERP?
- How many mandays will be cut short because of the utilized process of transferring materials?
- How effectively will the stock availability be optimized and how will this reflect to the profit of the company?
This and many more questions will be answered in the coming months - the accumulation of data helps to analyze and optimize the whole production process and isolate occurring problems.
The major advantage of properly integrated ERP system for organizing production is the constantly increasing in time added value.
We are extremely glad of stepping into this direction and choosing TOWERP for our partners. We are still studying some of the new functionalities but the positive effects are already visible. We are awaiting even more optimistic results in the future thanks to this implementation and we are confident to face new challenges.
Nikola Harsev, Production manager, Proto Ltd.
Company profile: Proto Ltd. was founded in 1990 in Haskovo as a knitted fabrics producer. In 2003 their activities expanded with a new factory for dyeing and finishing and the quantity of finished goods reached 100 tons/ month. In 2007 the owners found another base in Yambol, a new and modern factory for finishing loomstate fabrics with capacity of 15 tons/ day.
Industry: Textile
Company size: Mid-sized
Location: Uzundzhovo (Haskovo), Plovdiv
Production organization: TOWERP